There are a number of dedicated makerspaces throughout Sydney that'll teach you just about anything, from sewing your own leather goods to basket weaving, toolmaking and pearl knotting. With a little bit of practice, you could soon be part of a growing community of passionate local makers.
Meet the craftspeople and small-time business owners dedicated to making products from scratch, here in Sydney
Words Emma Joyce, Emily Lloyd-Tait & Juliana Yu
Photography Daniel Boud
↑ Annie Coulthard
FABRIC ILLUSTRATOR
Annie Coulthard makes tea towels that are very different from the ones you’d find at Target or Ikea. Sure, they’re cotton, rectangular and “meant to get dirty and have gravy on them”, but these ones don’t come in gingham and polka dot – they depict beloved Inner West buildings from the Petersham Water Tower to the legendary Marrickville Pork Roll shop. Coulthard, who moved here from the UK 20 years ago, married her passions for craft, Brutalist architecture and this particular form of napery into a budding business, selling her creations on Etsy, at local markets and at the Museum of Contemporary Art’s store. “I love the urban grittiness of this area,” she says. “I love the juxtaposition between celebrating a place on a tea towel with pictures of buildings that are not ones that people normally celebrate.” After taking photos of her chosen subjects, she reworks them digitally into the 2D, black-and-white renderings that have become her distinctive style, then, partnering with Arcade Screen Printing in St Peters, she transfers the images onto fabric. “It was a lot of work finding that ethical supply chain at the beginning, because I didn’t know anything about printing or making tea towels. I’ve sourced 100 per cent organic tea towels from India only because there are none in Australia at the moment, and I only use water-based inks, which are more environmentally friendly because you don’t need solvents to clean the screens.”
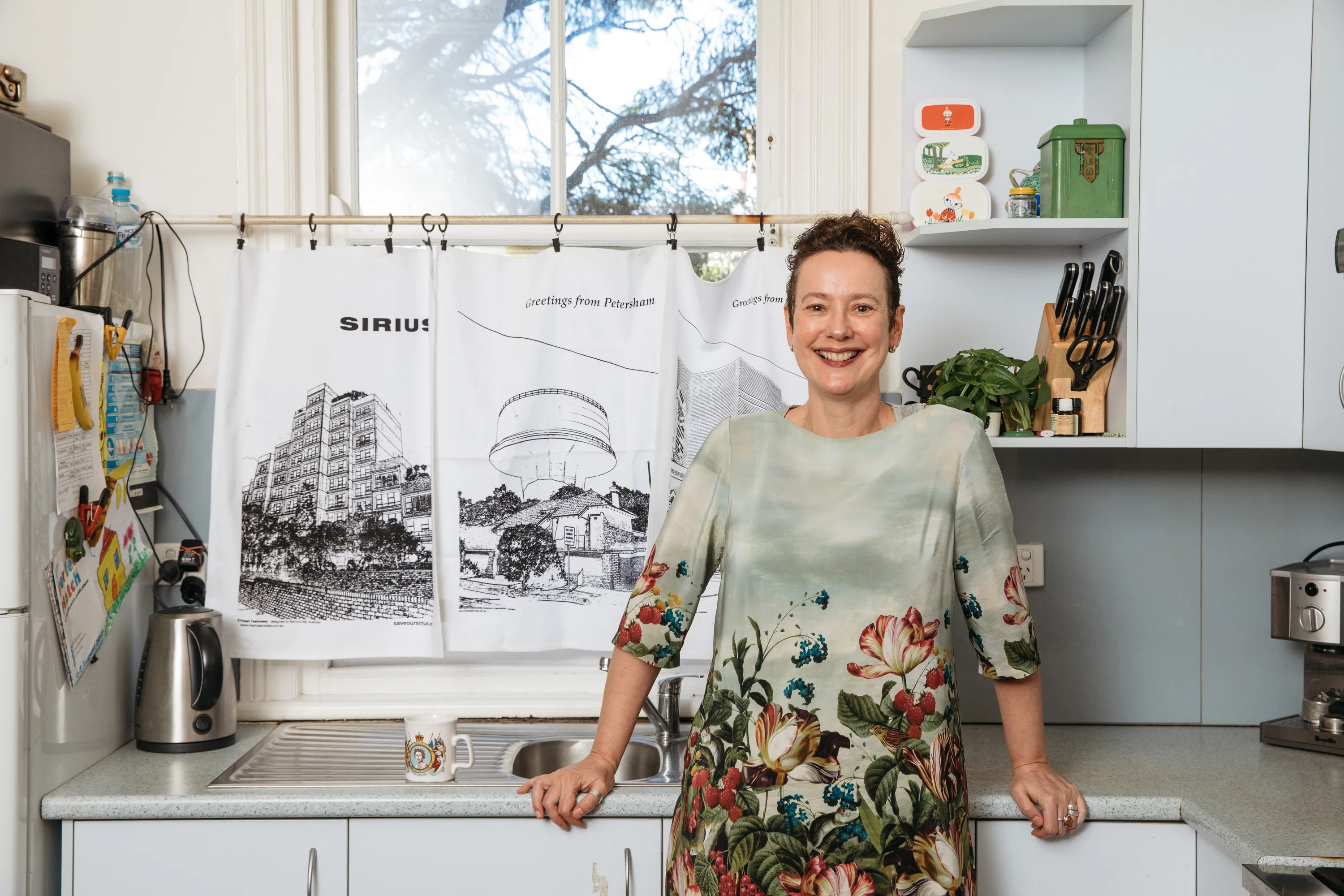
Community and collaboration are things Coulthard believes lie at the heart of being a start-up maker in Sydney. She’s currently running a fundraiser for the Save Our Sirius campaign, donating all profits from towels depicting the retro-futuristic public housing complex in the Rocks. So why tea towels as a medium? “They’re portable works of art. I’m choosing things that are my aesthetic, not just traditional icons like the Opera House. Some people are like ‘why are you celebrating that ugliness?’ But others really connect and have emotional responses to seeing their favourite building – the Marrickville Pork Roll one has definitely caused the most laughter, because people just don’t expect to see that on a tea towel.” Juliana Yu
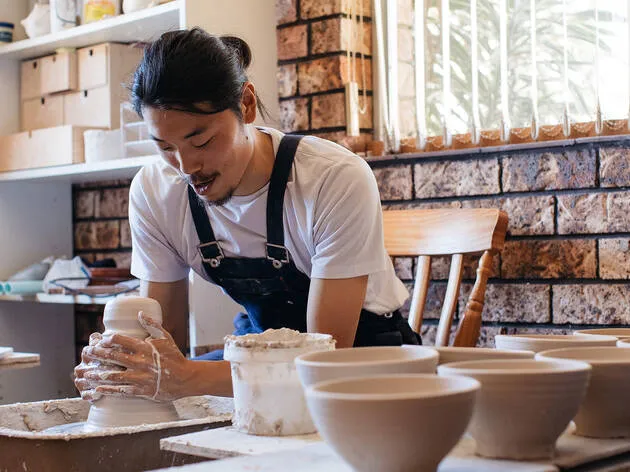
Ion Fukazawa
CERAMICIST
To be an artisan in Sydney takes drive and skill, but a whole lot of space in your parents’ Allambie Heights house helps. As does word of mouth. This has proved the winning formula for Sydney ceramicist Ion Fukazawa, whose bespoke stoneware plates you may have eaten off at Ester or Sixpenny. The 27-year-old ceramicist started out playing in Sydney ground clay as a kid, before attending high school in Japan where the 3D art teacher was a chilled-out American with a penchant for pottery. Fukazawa doubled down on his clay skills at COFA where a graphic design degree with a sideline in ceramics gradually morphed into a full-time career. For a while, Fukazawa tried living in the Inner West, throwing pots by day in a shared studio space with other Sydney makers like his colleague in clay, Milly Dent, and working nights at Japanese restaurant Izakaya Fujiyama. But in order to make it a full-time endeavour he needed space and time. He moved into a downstairs room in his family home and set up a glazing room and kiln, bought for $800 on eBay, in the garage.
“The resurgence of craft is an opposite movement to everyone getting on the computer”
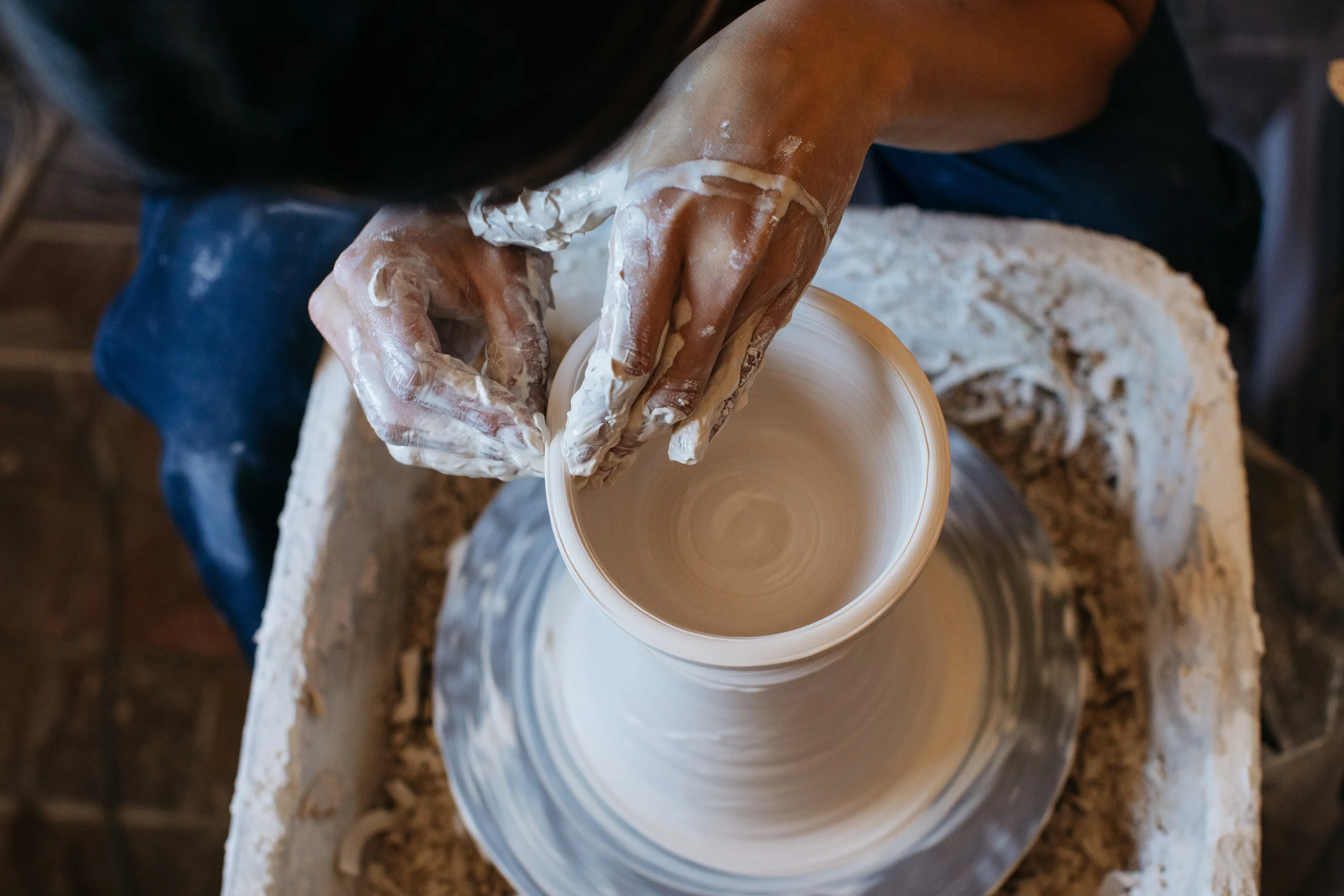
On an overall business scale the start-up cost is very low compared to something like a restaurant,” Fukazawa says. “If you’re doing it as a hobby, then it’s very expensive. But if it’s going to be a business then it’s comparable to getting an app made.” He stresses that being a maker in Sydney is not a particularly solvent life. “You really have to like what you’re doing and you get paid by your satisfaction more than money.” Fukazawa describes the handmade ceramics market as “niche but growing”. “The resurgence of craft is an opposite movement to everybody getting on the computer. At the same time Sydney is booming with restaurants and now they realise they’ve all got the same plates, because there are only a couple of companies that import ceramics, or they’re the standard white ones. That’s where my job comes in. I can make plates for restaurants that want specific things to differentiate themselves.” In the instance of Ester, Fukazawa incorporated the ash from the restaurant’s wood fired oven into the glaze as an unpredictable and unique design element. In addition to making hand-thrown tableware for restaurants, he also has a core range of stoneware cups, plates, bowls and pots under his Mukumono brand, which you can order online or from the Finders Keepers Market in Sydney on December 8-10. Emily Lloyd-Tait
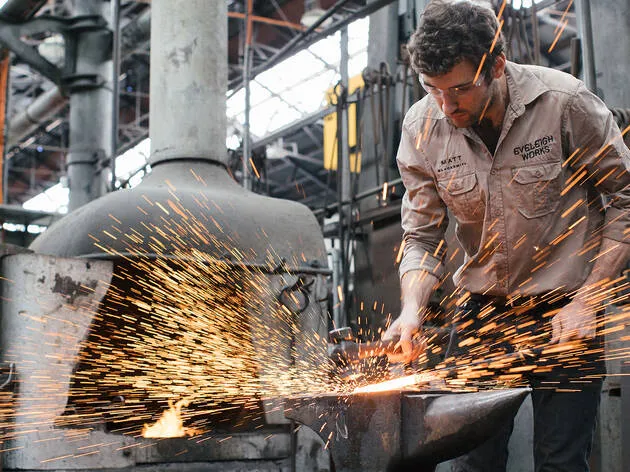
Matt Mewburn
BLACKSMITH
Over the chink of metal, the hum of an industrial blower and a roaring 1,400°C fire, Matt Mewburn explains that though he’s only 29, he’s probably been a maker since he started crawling – from tinkering in the shed at his Frogmore home in rural New South Wales to his first business as an electronics manufacturer in Sydney. “We were probably one of the only places in Sydney manufacturing printed circuit boards from scratch and building them by hand. Most of it’s now automated and done overseas,” he says. Today, Mewburn is one of half a dozen full-time blacksmiths working in Sydney at what he says is the best venue for it in the world. Eveleigh Works is a functioning makerspace in Redfern that utilises the machines and light-filled heritage site of the old locomotives workshop. Though the products Mewburn is making are more architectural and sculptural than the metalwork forged here three decades ago, they’re using some of the old machinery and repurposing steel for hammers and tongs. “Traditionally blacksmithing was a very clandestine art – people didn’t tell others what they were doing, or how they were doing it. It was very generational and you didn’t want to give away the secrets.”
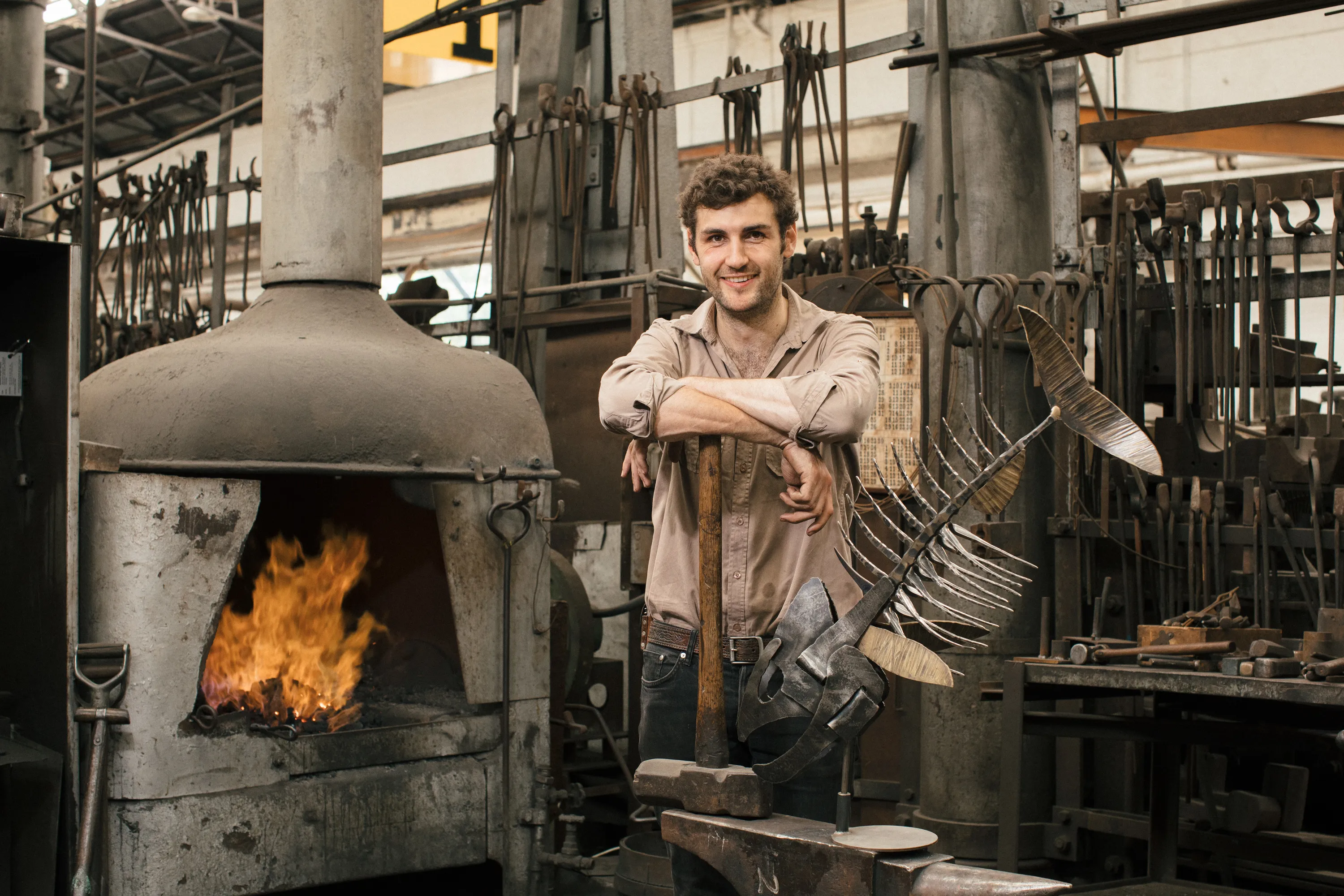
Today, the ironborn community is more supportive and they share trade secrets at specialist festivals each year, like Ironfest in Lithgow. Mewburn also teaches introductory blacksmithing classes. “We get a lot of young people, older people, people without any skills… People have this disconnect, they don’t get to be physical in their jobs, so they’re looking for an outlet for that.” Monday to Friday, Mewburn works for clients as varied as hospitality giant Merivale to homeowners looking for functional and decorative ironwork. He also crafts hand-forged Damascus steel axes, which sell for upwards of $1,000. The skills he’s picked up from various TAFE courses and six years of trade are passed on through weekend workshops. “Blacksmithing is amazing and I love it. Will I be doing it in ten or 20 years? I don’t know. If it’s still serving [a need] and interesting, then yes.” Emma Joyce
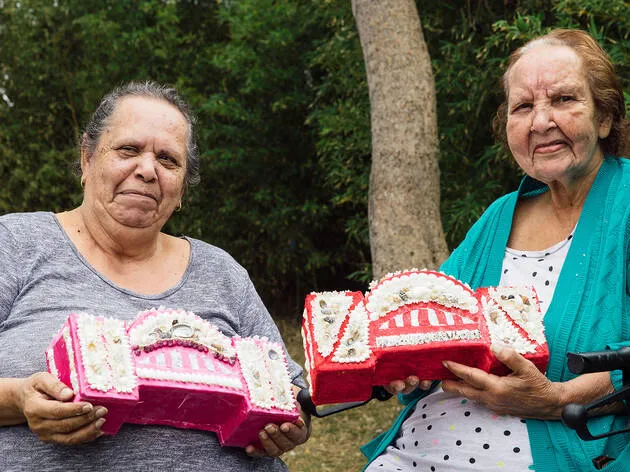
Esme Timbery & Marilyn Russell
SHELL WORKERS
Bidjigal elder Esme Timbery has been creating art with shells since she was a little girl living in the unemployment camp Happy Valley in La Perouse. “I used to go with my mother and aunties to Kurnell every Monday morning to pick shells,” says the 86 year old. Today, Timbery is a renowned, respected, award-winning artist whose works are part of the permanent collections at the Art Gallery of New South Wales, the Museum of Contemporary Art (a wall of 200 shelled slippers) and the National Museum of Australia. You can also buy her artwork, including the popular shell-adorned Sydney Harbour Bridge shape, for $300 at the Blak Markets on Bare Island and Barangaroo. Esme’s eldest daughter, Marilyn Russell, works alongside her mother to make the products, from bridges to baby slippers and jewellery boxes. They also teach workshops to Aboriginal and non-Aboriginal groups, facilitated through First Hand Solutions Aboriginal Corporation. Timbery prefers to sit in her armchair as she separates shells into neat mounds of starry shells, Chinaman’s Hats, buttons and fingernails – all nicknames for the shapes found at local beaches such as ‘Pussycat Bay’ (Cruwee Cove). Marilyn prefers the kitchen table, where she’ll pile all the shells together and sift her hands through the dusty mix as she’s decorating. “It’s something you can’t plan,” says Esme, who worked as a ward’s maid in a hospital before getting into shellwork once she was married. Marilyn adds, “My great, great granny Queen Emma used to make shellwork and sell that to the tourists. She made a Harbour Bridge and it’s still in England today, but that was for survival. It carried on with each generation and now I think it’s a beautiful tradition. We’ve got to keep it going because it’s something precious to our culture in La Perouse, as saltwater people.”
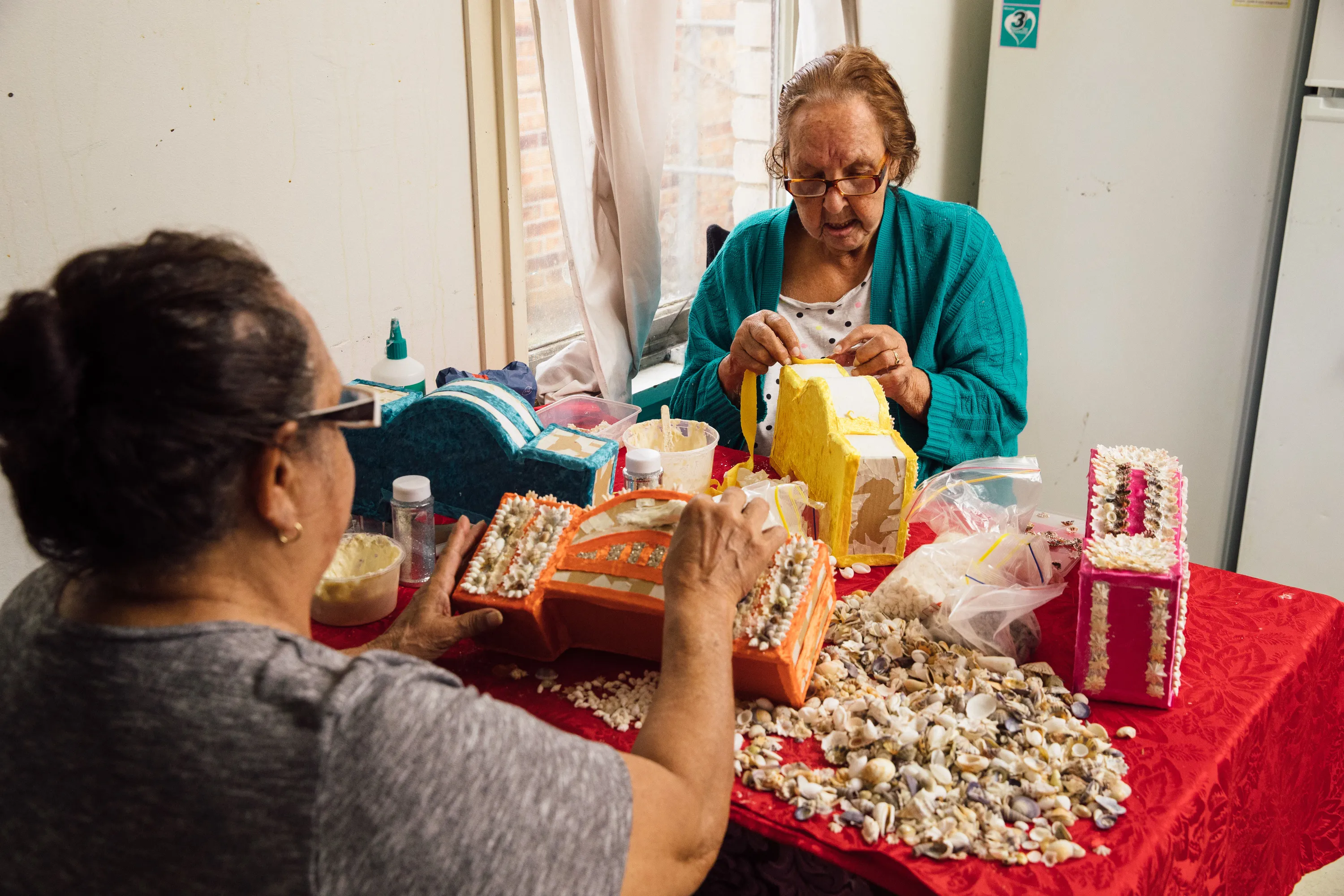
Russell is 65 and her daughters also create shell artwork, but only when they have time. It can take a full day to create a Harbour Bridge shape from scratch; first cutting up cardboard, gluing the structure, decorating it with velvet, satin or cotton and finally adding the shells and a touch of glitter. “When I look at the final picture, I love it,” says Marilyn. “I think I’m pretty good because I had a good teacher,” winking to her mother. Shell working was a skill shared by many Aboriginal people in La Perouse who used to sell souvenirs on the former tramline route called ‘the loop’, a tourism destination in the 1950s and ’60s. However, the Timbery family story – including Joe Timbery who, in 1954, presented his boomerangs to Queen Elizabeth II – means it’s important for the pair to share their skills. “It’s vital that we keep this going,” says Marilyn. “We call it our healing, because you can close everything off around you.” On November 11, Esme and Marilyn will be teaching a shellmaking workshop at Bare Island (11am-3pm. $80). You can also find their work at the Blak Markets (10am-4pm, Sun Nov 5). EJ
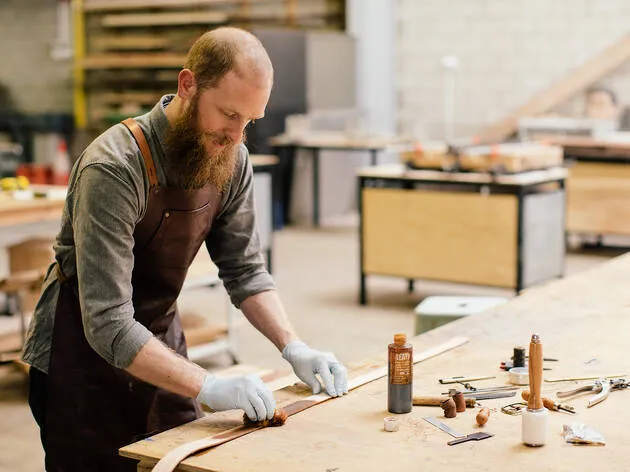
Iain Finlay
LEATHERWORKER
Ten years ago, Iain Finlay went back to university to retrain as a designer after working in jobs ranging from electrical engineering to cooking in a Japanese kitchen. “In all my roles I wanted to be able to make something to help people,” says the fulltime industrial designer, who also runs leather making workshops at Makerspace &Company and sells leather belts, folios and wallets under the brand name Iain Designs. “One of the things I love about leather is that sense of honest material. I haven’t yet been able to explain why you get that reaction from people where they just want to smell it or touch it, whether it’s nostalgia or something more deep rooted.” Working from his home in Paddington, Finlay has created one-off products for people who share that appreciation for natural materials and craftsmanship, including making a bag for the owner of Deus ex Machina’s first motorbike, Dennis Lindsay, who runs the Better Living Index blog, and he’s developing glasses cases with eyewear maker Chris Savage. “While it might not seem that using animals skin is necessarily environmentally sustainable, at the very least it is making products that are going to last a lifetime.”
“Plastic deteriorates. Leather starts its life when you
buy it”
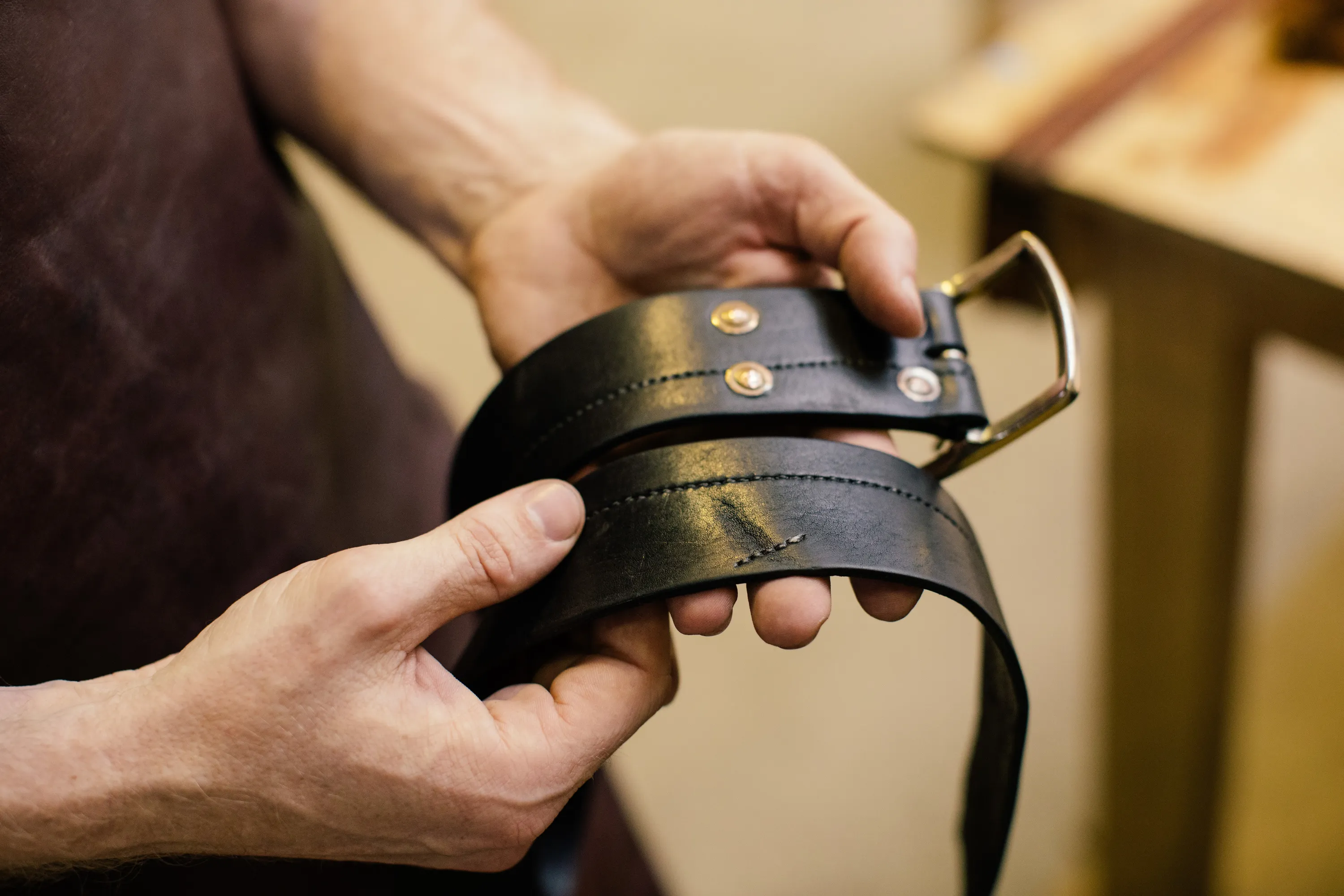